Within the context of rare, hybridized thinking, Alex Rasmussen has very little competition. At the moment, he is the only one who combines fine art and functional practicality through the medium of anodized aluminum. Called a progressive metalsmith, he is the president of Neal Feay Studio, the company his grandfather founded over 70 years ago. The Studio has created over 200 products that range from architectural surfacing to luxury furnishings, to medical and audio components.
With aluminum, he is creating new dimensions of luminosity and is the global leader in its creative use. Right now, the Studio is working with Louis Vuitton and Design Miami, as well as Holly Hunt and Opening Ceremony. His aluminum work has been often been said to obscure the boundaries between artisanry and art.
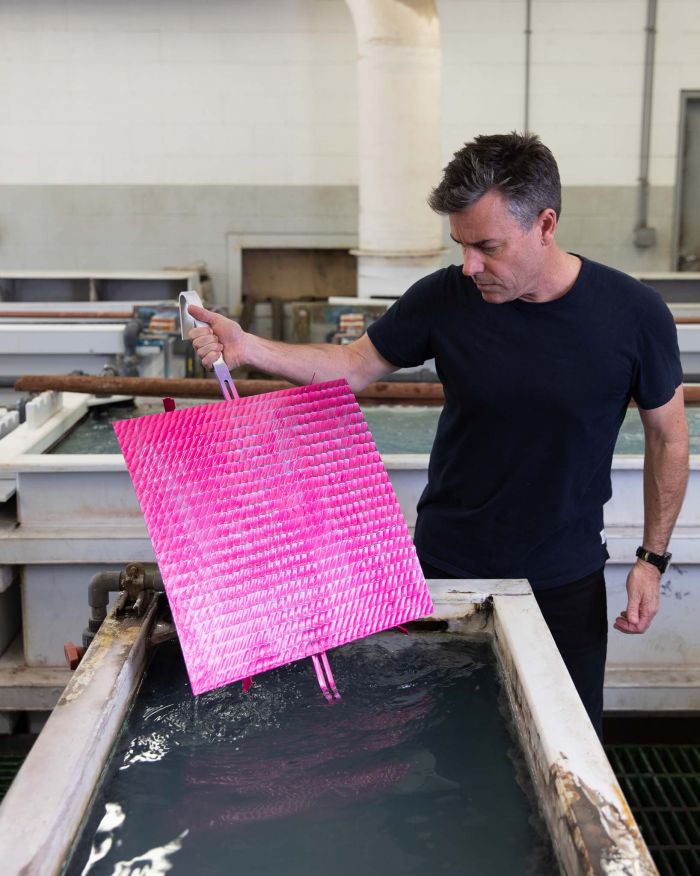
In a recent article, he was asked why he used aluminum as his major creative material. His answer combined the vision of the artist with the voice of the structural engineer. “When you look at a piece of anodized aluminum,” he said, “you are looking at light going through a sapphire crystal, filled with dye and then hitting aluminum and bouncing out. The aluminum under the anodization is reflecting through that anodized surface. There are so many possibilities in this reflective beauty.”
While in his studio in Santa Barbara, I asked him more questions about his strategic thought processes that allow him to create exceptional art from conventional material.
JL: It takes a certain vision to combines artistic with pragmatic— someone who can take an industrial skin and create something different with it. In your case, you have allowed anodized aluminum to evolve into a more fluid, reflective, and refractive dynamic. Your generational evolution (from your grandfather who founded Neal Feay Studio, to your father to you) becomes both a product and a personal evolution also. Do you see, within the context of your work, these evolutions merging?
Rasmussen: That’s an interesting notion. I have to say that I benefitted from the advent of technology that my grandfather and father did not have access to. My grandfather was very much a self-made man and focused on the sales, while still maintaining a very high sense of style. He explored the beauty of the reflected nature of aluminum anodizing in the early 1940's and in 1946, he developed multi-color anodizing. He invested in graphic design and created our logo in the 1950's. As for my dad, he constantly did personal projects, and making things was always a part of growing up in my house.
JL: You mentioned Lalique glass in one of your interviews. I have an original Peroquette Lalique vase — the glass, when the light hits it in a certain way, reflects and refracts diverse color prisms, making the vase not look like glass at all, but a container of rainbows. Is that one of your goals -- aluminum skins to become a kind of product dualism, something that is aluminum but doesn't seem like aluminum?
Rasmussen: I met Marc Larminaux, the creative director at Lalique, through a mutual friend and got the chance to go to Rue Royale and look at how they work with the material. Lalique was taking a humble material, glass, and manipulating it with finish, color, and form to create luxury pieces from sand.
Lalique and I have that parallel. Cutting glass and aluminum have some of the same constraints. Any form you see in a Lalique, we can do. We’re trying to introduce the world to new personalities of aluminum. Simply, we’re trying to introduce a real character through dimensions of aluminum that no one else has seen. That's because no one else has pushed the concepts that far.
JL: Are there ways you are planning on using anodized aluminum in yet ever more diverse ways in the future? If so, what are some of them?
Rasmussen: Neal Feay Studio has already been doing quite a few large-scale commissions for façades. The first façade work was for Louis Vuitton and we continue to do a lot for Vuitton in North America. Also, we’re doing a large cladding project on Pacific Coast Highway for a major car collector. Applying an acute level of precision to a large-scale building and seeing the way light plays off the building is such a great project. At the same time, we’ve been working with some incredibly talented artists on how to create art within our anodized surface itself.
I’m extremely interested in how architects like Herzog and de Meuron are bringing in artists on an architectural scale. Rather than just making 30 x 40 aluminum paintings, I th
The Wave, Anodized Aluminum Art, In Production
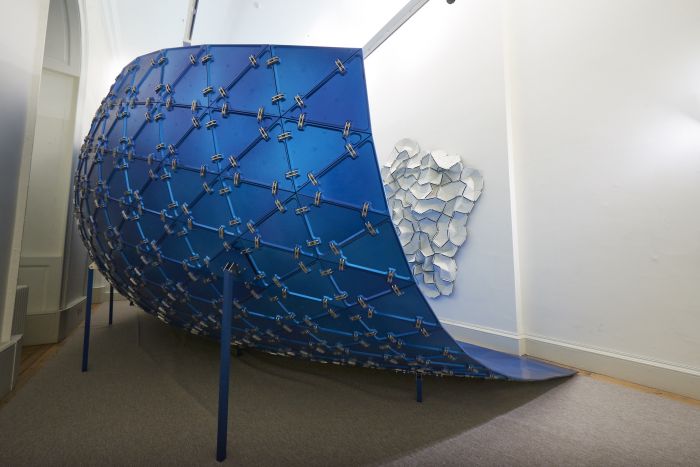
The Back Of The Wave, from Anodized Alumnium
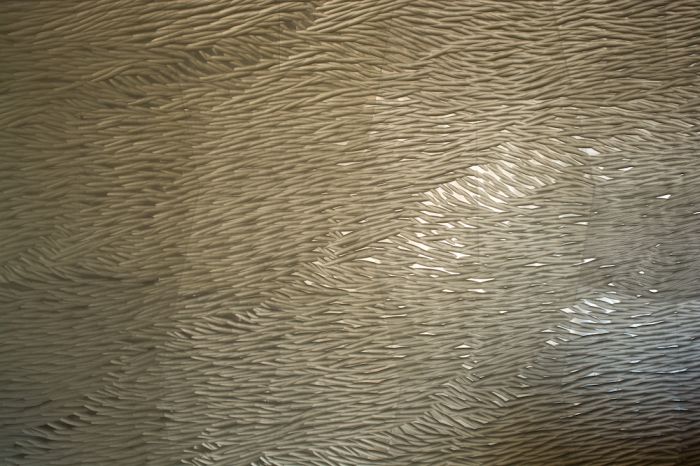
Interior Wall Design from Anodized Alumnium
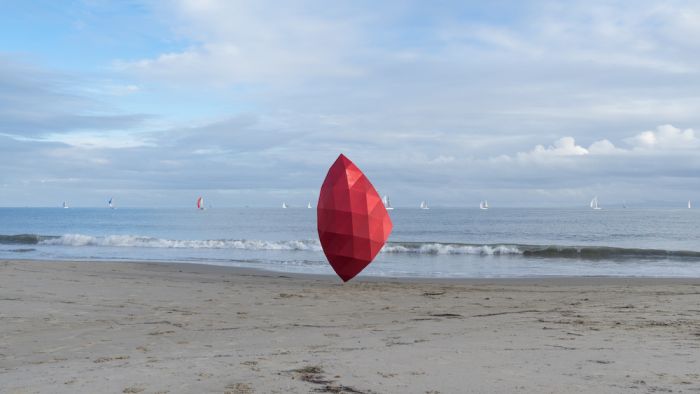
Spinnaker Design For Water Sports
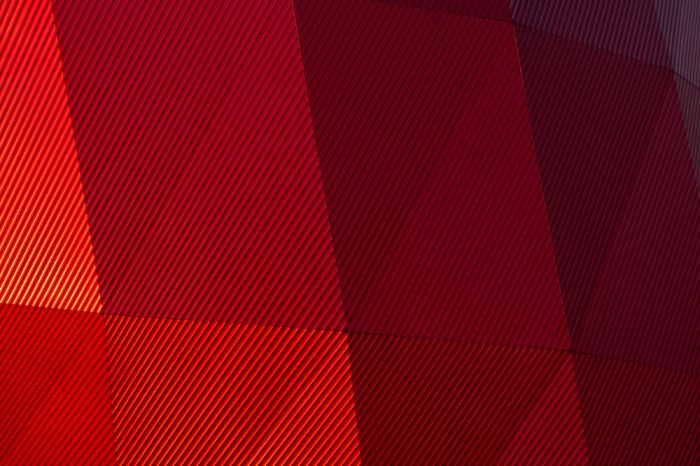
Close-up, Spinnker Design from Anodized Aluminum
